Soaring Above September 2022 at TyRex
Amit2025-03-11T14:47:25+00:00The TyRex Technology Family took off and flew through the month of September dropping exciting features along the way. A TyRex Family Member at Saber Data received special recognition, Arctos broke down 3D design guidelines for better 3D printing, and iRex cable engineers harnessed the power of split sleeves to impress a client in the automotive industry.
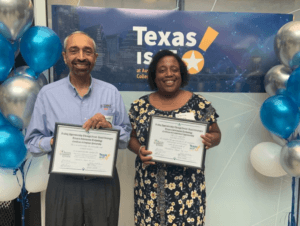
TyRex Family member and Saber Data software developer Gloria Walls was recently recognized by Austin Community College (ACC) at the Texas is IT (TXIT) Recognition event as the second student to have completed their apprenticeship program and having joined the company where she completed her apprenticeship. We are very proud of Gloria and appreciate programs like TXIT that connect professionals with companies like ours!
“Thanks to the ACC and the TXIT Apprentice program, Gloria was able to improve her skill set and advance her career while our Software Development and IT department was introduced to an outstanding individual who’s a great asset and an excellent fit for our company’s culture. A win-win solution!”
–Satwinder Kahlon, President Saber Data
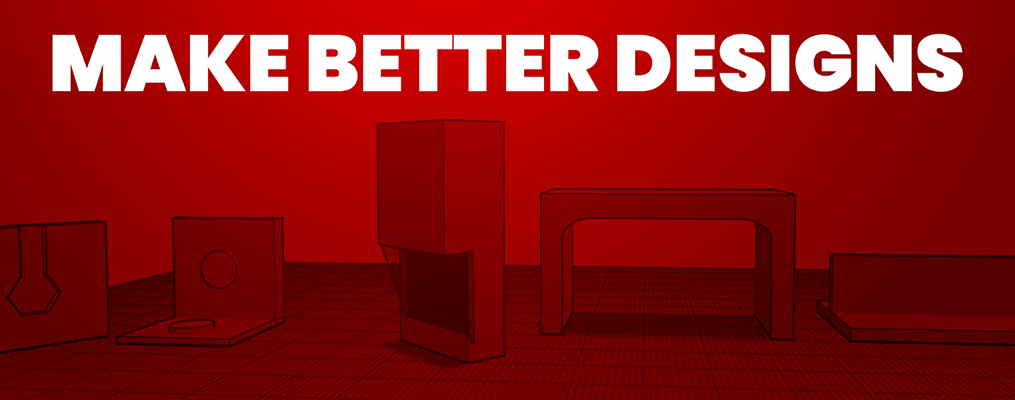
Arctos and the larger TyRex family have spent years developing our 3D design and production processes to great effect. Through the introduction of additive manufacturing, we’ve avoided supply chain issues, reduced the weight and unit prices of products, and quickly iterated on designs in ways once thought impossible. In this time spent developing, we’ve come to rely on a set of design guidelines that help keep our printed components as functional as possible. In this guide to making better designs, we’re breaking down everything needed to know including gradual transitions, overhangs, venting, threads and more.
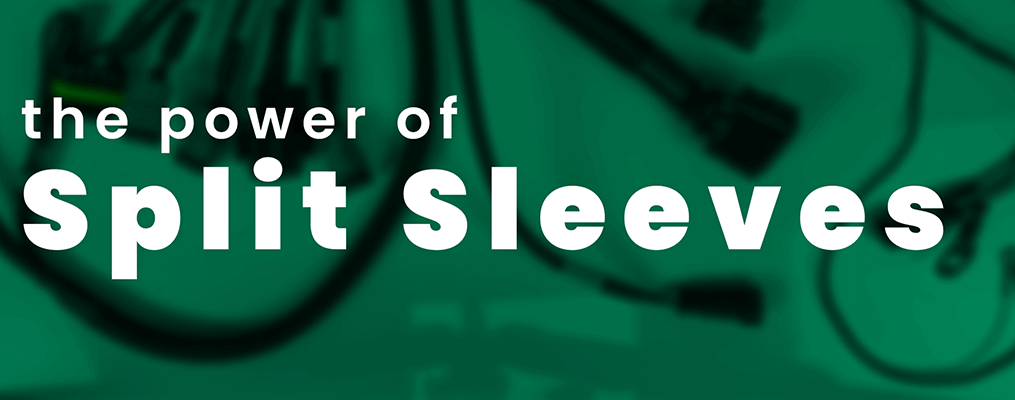
A client in the automotive industry had a complex cable harness with an extensive variety of terminations required. Team iRex took the original design that contained nearly 30 different cables that needed to be pulled through non split tubing prior to termination and proposed that the cable be made with a split sleeve. This way, multiple teams could terminate in batches before the cable harness was sleeved. Being able to have teams focus on specific terminations improved consistency and saved over 1,000 man hours over the course of the project.